April 9, 2020 - (Ottobrunn, GER) In 2014 Fabian Reuter and Johannes Biechele set course to create an industry leading, long-lasting drive system that would enhance the e-bike experience. Their award-winning Evation Drive System is now a global leader for performance e-road and e-MTB bikes.
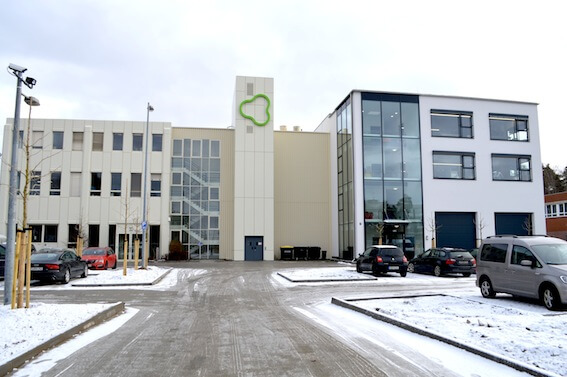
They opened up shop in Ottobrunn, near Munich, in a factory which used to manufacture rocket engines. By 2015 the first e-bike drive prototype was developed which lead to full production in 2017. Quick rapid growth, saw them build an addition to the current facility to become their main manufacturing plant and global headquarters.
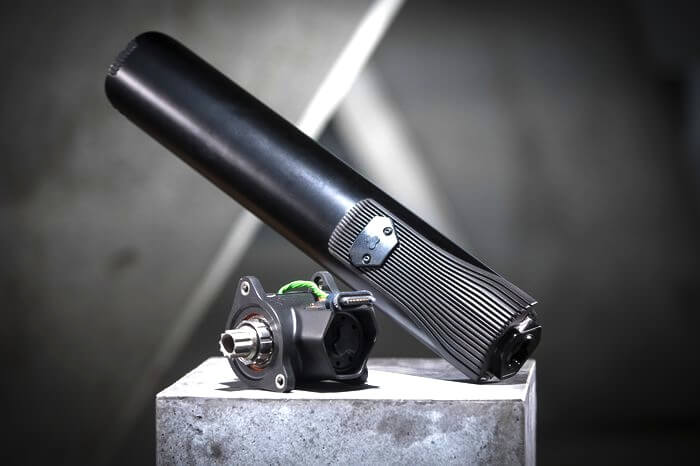
Fazua’s e-bike drive system is a complete, lightweight unit consisting of a bottom bracket, motor and battery. The entire system weighs 4.6 kg and is completely integrated into the bike frame for a seemless and streamlined appearance. It provides a traditional ride experience with subtle pedal-assist as the motor is designed to disengage with speeds above 25 kph. The maintenance-free drive system can also be fully removed allowing the bike to revert to a traditional bike.
Fazua’s “Made in Germany” approach allowed them to maintain full control of their growing business. Viewing quality control as imperative to success, they insured that R&D, testing, production, assembly, shipping and service all stayed within their factory walls. They sourced out manufacturing for their high quality parts to some of the best German and international companies.
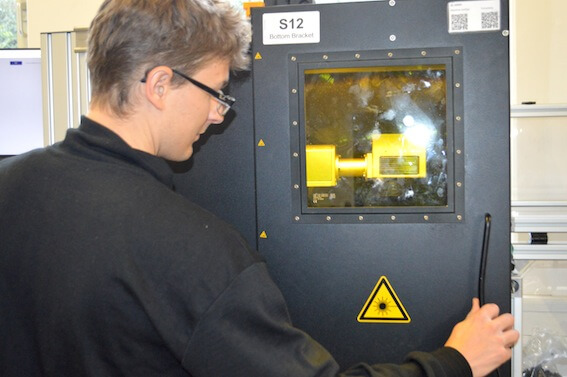
The factory is set-up with independent rooms to handle each specific component of the Evation system as it arrives from the manufacturers. Bottom brackets, motors, control units, locks and batteries are all assembled and tested by highly skilled staff. Lasers are used to quality check the parts while serial numbers are recorded for future reference as needed. Once completed, they are package up and shipped directly to customers.
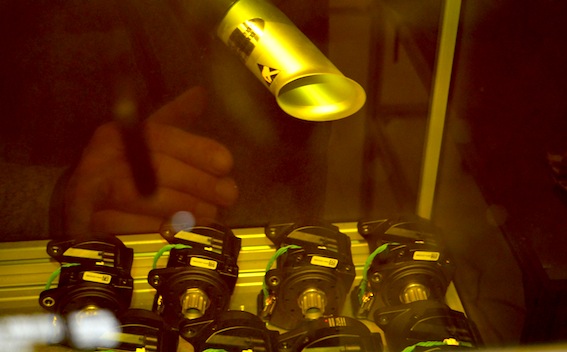
A dedicated testing room provides space for the drive systems to be set-up on a station bike, connected to a computer and then tested to real world conditions and beyond. Data on motor performance under varying conditions and battery consumption is just some of the data analyzed using specific software.
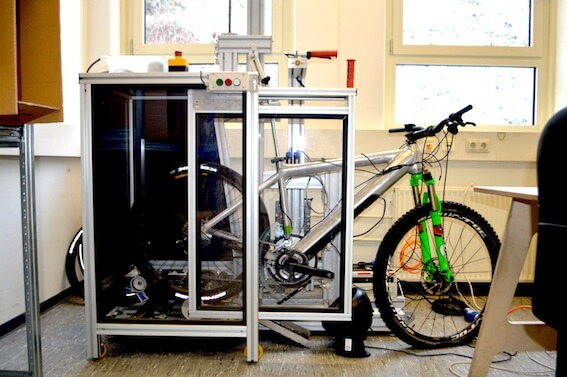
Being unconventional for a young company and wanting to maintain the whole value chain in-house, the fast pace of the e-bike industry has presented challenges. First off, funding was required to assist with manufacturing operations in particular with acquiring and maintaining necessary levels of materials. Next was getting their drive systems to their customers.
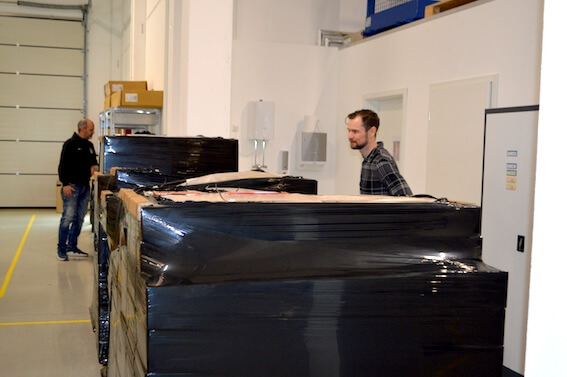
“One of the challenges we didn’t expect was that it would take so long for bicycle manufacturers to get their special frames manufactured to work with the Evation system. This caused delays in shipping from our end. We now have about 40 bike brands using our e-bike drive units, which meet and even exceeds expectations,” commented Reuter – see our video interview with him below.
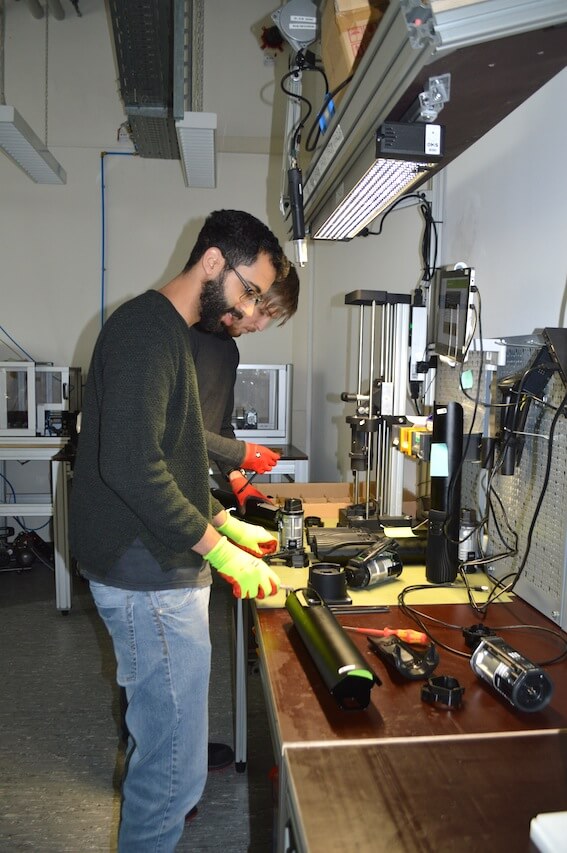
The top floor of the warehouse is the R&D department. Engineers, specializing in areas such as mechanical, electrical and embedded software have a bright, open space in which to create. “We have been able to source many engineers from Germany, but we also recruit outside of the country for hard to find specific skilled workers, like embedded software engineers,” explained Reuter.
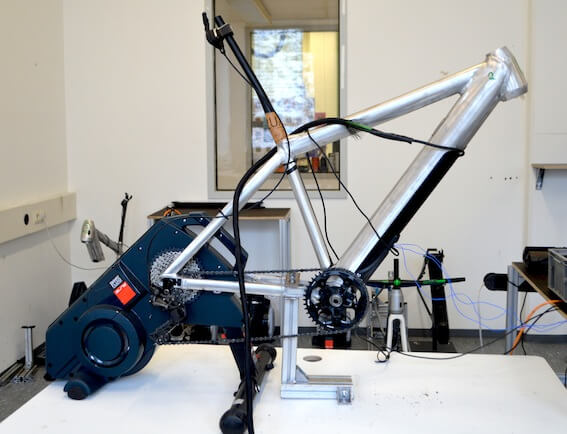
The Evation system is built to last for thousands of hours, with replacement parts and servicing available if needed. “Building a product to last was a big part of our philosophy. Also, if the drive unit ever becomes un-useable, it can easily be removed from the frame and you have a regular bike. This makes us unique among the other brands,” he continued.
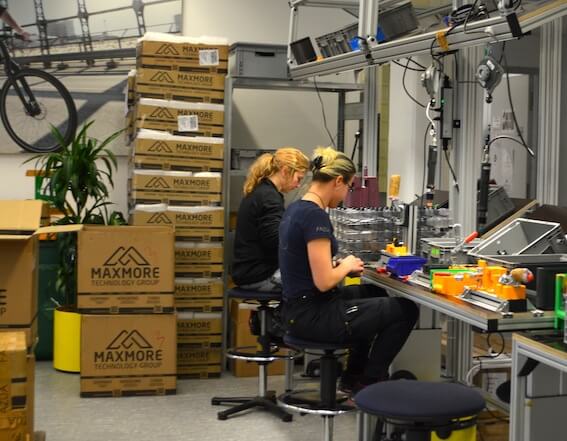
In early October 2019, Fazua GmbH announced a EUR 12 million loan from the European Investment Bank (EIB) which assists innovative companies in its quest to boost the competitiveness of the European economy. The funds were intended for expansion to new territories and for research and development activities and soon after Fazua officially entered the North American market.
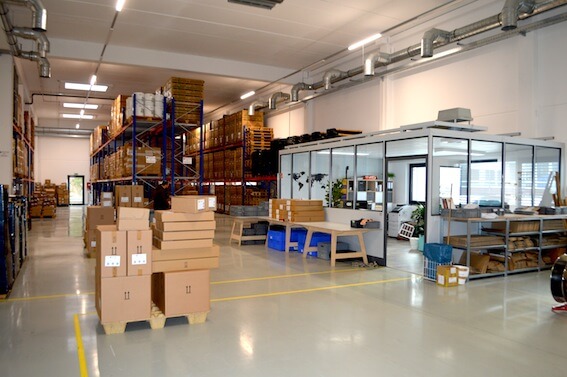
In December 2019, the USA and Canada became the first non-European countries where their products would be available. To help with their growth in both markets, Fazua partnered with bicycle industry distribution giant, Quality Bicycle Products (QBP), to take on servicing in both countries.
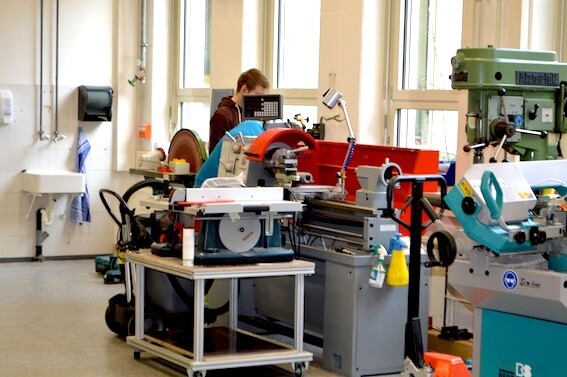
With the fast paced growth in the e-bike industry, Fazua finds itself ready to meet existing and future demands for their product. Since our visit they’ve acquired a big 3D-printer and a huge CNC machine says Reuter. Improvements to their software are also coming which will be compatible with all other brands – read more about their recent Black Pepper announcement here. Digital products and customization options are in the works as well including specific systems with unique benefits for riders with different needs.
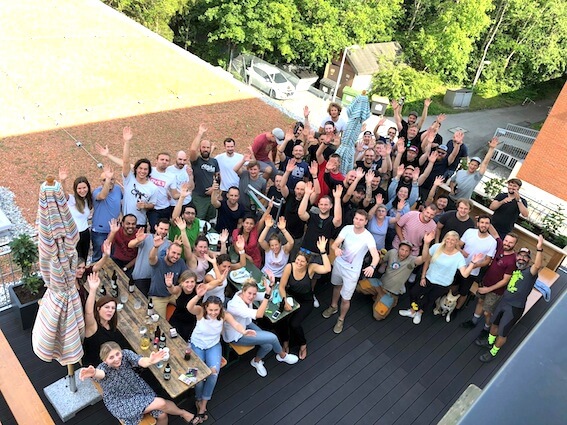
They currently produce about 100,000 units per year with enough space at their site to add another assembly line when needed. “The current space should be sufficient for the next two years… after that, who knows,” commented Reuter.
Winner of the prestigious Design & Innovation Award, a benchmark in the cycling industry, multiple times, Fazua has established itself as an innovative e-bike drive system global player.
So where did the unique company name of “Fazua” come from? In the local Bavarian dialect it means “go on” or “get going” and while the locals pronounce it a bit differently, the meaning and direction are the same. Fazua GmbH seems destined for more success on their e-journey ahead.
For more information visit here.