November 29, 2023 - As e-bikes and climate change continue to make headlines, Taipei Cycle, one of the world’s leading cycling industry shows, is expanding its focus on electrification and sustainability in the lead up to its biggest event ever next year from Mar. 6-9, 2024.
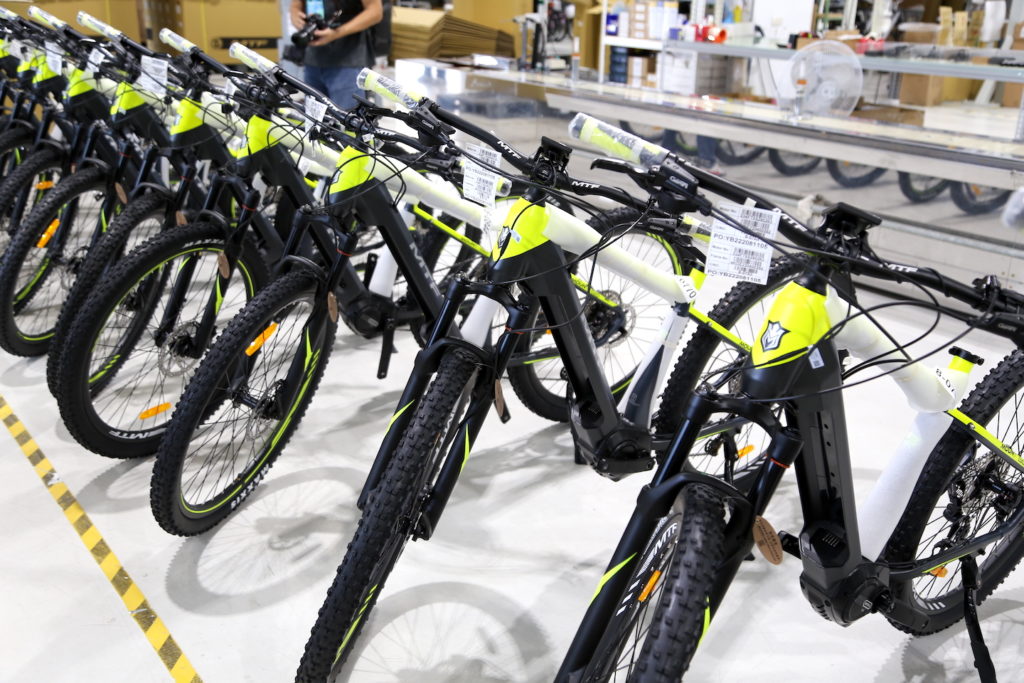
The need for electrification is a driving force in the ever-changing landscape of transportation, and the show organizers held a media tour to showcase their cycling industry and ESG (Environmental, Social, Governance) strategies to reduce their carbon footprint.
With a focus on green micromobility, the Taiwanese bicycle industry is keen to demonstrate its positive impact and leadership with respect to e-bikes, recycling, sustainability, and other environmentally friendly practices.
Our media tour visited the western coast of Taiwan known as a hub for the cycling industry, along with semi-conductors, electronics and plastics. These industries combine together to cement the country’s place as a key global player in the mid- to upper-end bicycle industry.
In this 3-part series, eBikes International presents an inside look at rising stars and established players as Taiwan’s vibrant cycling scene continues to expand and evolve.
Yota Cycles
Yota Cycles made its name producing rubber products for the skateboard industry, but in 2020 the company decided to branch out into e-bikes as demand boomed and the move aligned with their environmental philosophy. “E-bikes are an important sector to help reduce global carbon emissions,” commented company president, Walter Chou.
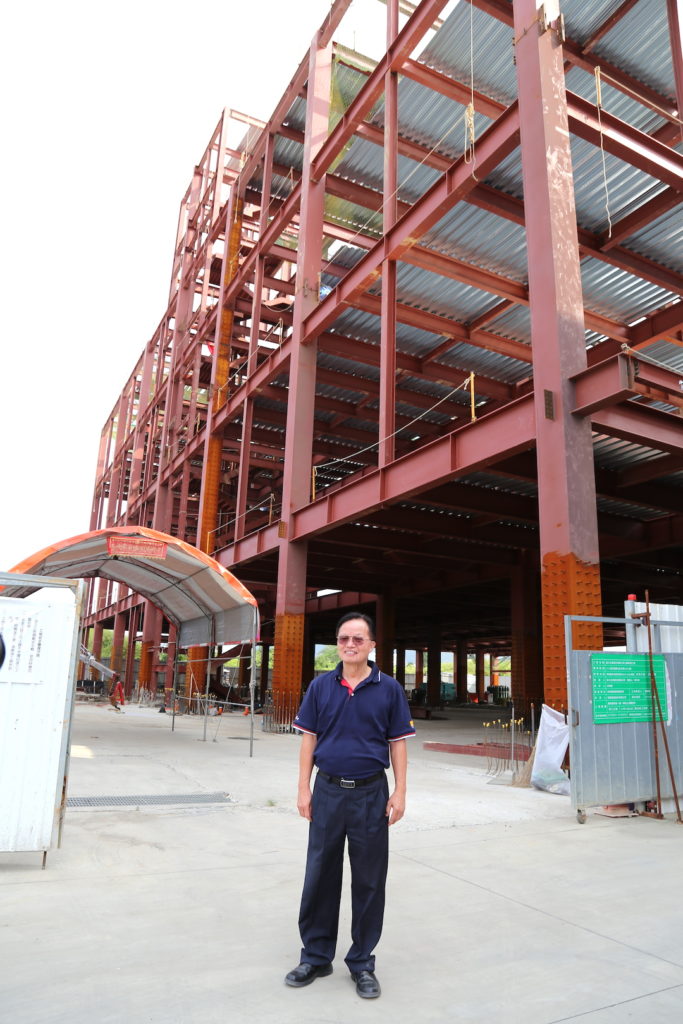
Despite the current downturn in business as inventories remain high, Yota is investing significant resources to increase its capacity and demonstrate its full commitment. Their current facility features two assembly lines that produce 250 e-bikes per day, but a $25 million US building expansion next door, will result in five assembly lines in 2024, which will substantially increase their capacity.
Yota is also opening a new factory in China to manufacture and paint frames and thereby complete their full-service assembly production goals.
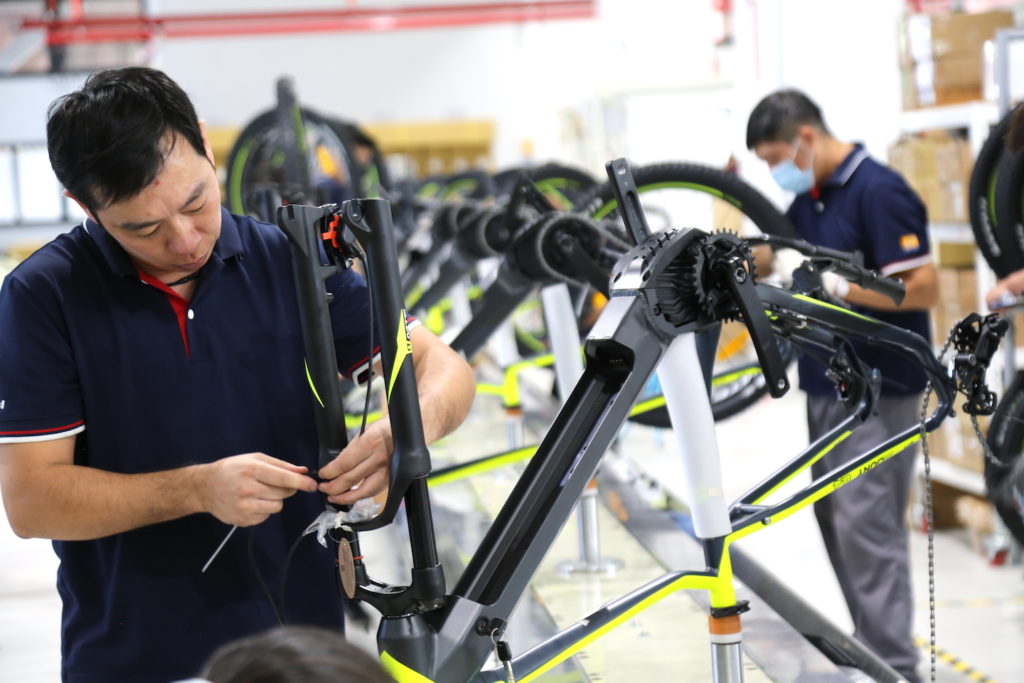
They offer both OEM (Original Equipment Manufacturing) as well as ODM (Original Design Manufacturing) services and are ready to design and build bikes for customers who require that aspect of the manufacturing process.
An additional benefit for bike brands is that they can specify virtually any motor in the marketplace and Yota can incorporate it into the assembly process of their e-bikes.
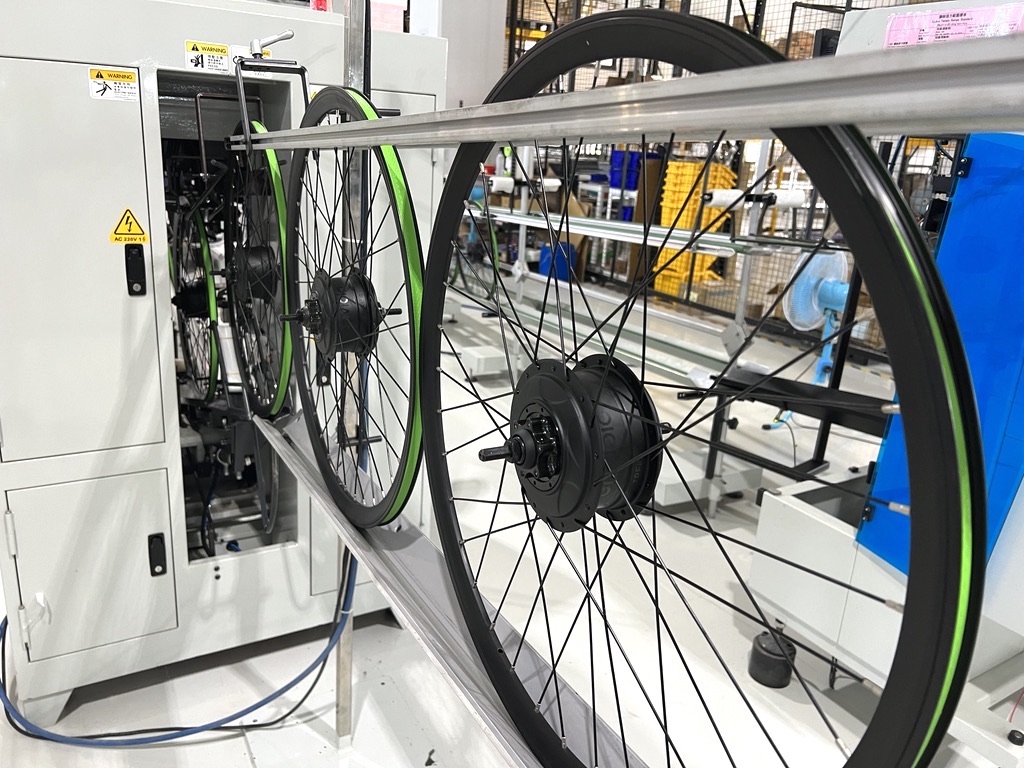
Also all wheels are built in-house on two wheel building assembly lines and e-bikes that require a hub motor are more easily accommodated as well.
Yota targets European business which accounts for a majority of their current annual sales of $8.3 million US. Customers such as Vélib’ Métropole Bike Share in Paris are important for sustained business.
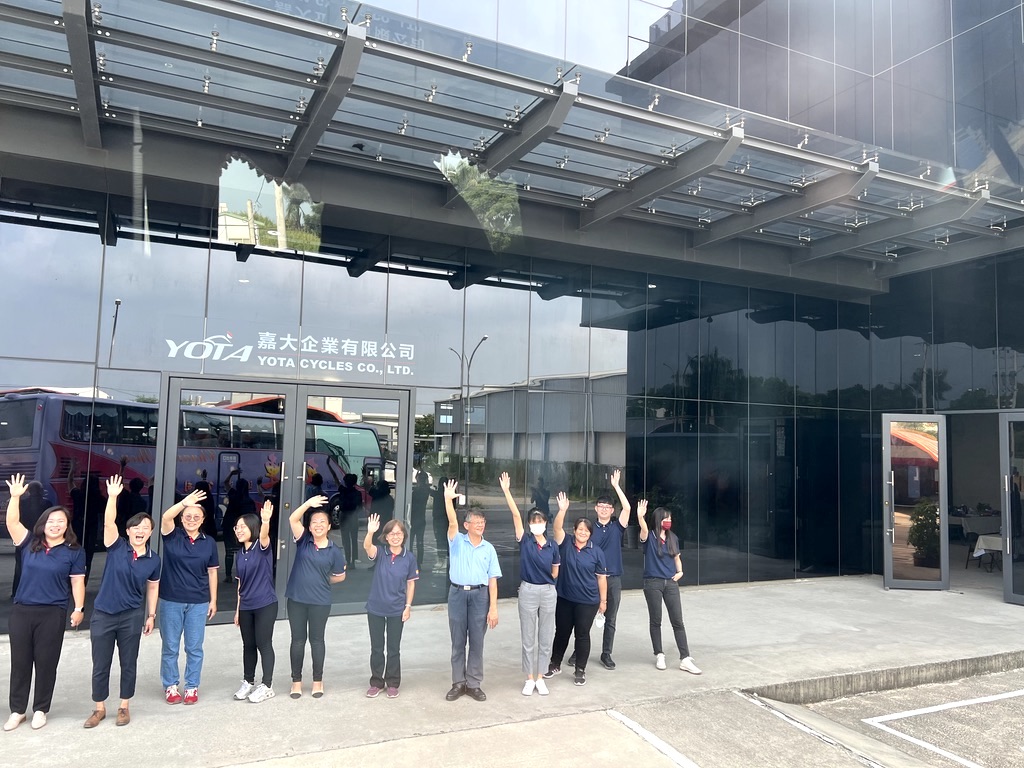
Next year, Yota is projecting growth of up to $40 million which is contingent on their new factory being completed on schedule as well as securing new North American customers.
The company’s environmental efforts don’t stop with building e-bikes. Yota is also taking into account its carbon footprint with their new construction and all glass will be Low-E, or low-emissivity, while the building will use solar panels to generate its own electricity.
Formosa Taffeta Co.
Formosa Taffeta is renowned worldwide for its quality fabrics that it supplies to many global sporting companies such as Patagonia, Nike, Columbia and Adidas. The company is also a supplier to the bicycle tire industry with brands like Maxxis.

As part of their environmental efforts and ESG strategy, it uses recycled fishing nets in their production processes which has become an important part of their program.
With Taiwan being an island with a huge fishing industry, there are significant amounts of fishing nets that are disposed of on the beaches and in the ocean all around it. With 640,000 tonnes of old fishing nets generated annually around the globe they’re an ideal item to target for recycling.
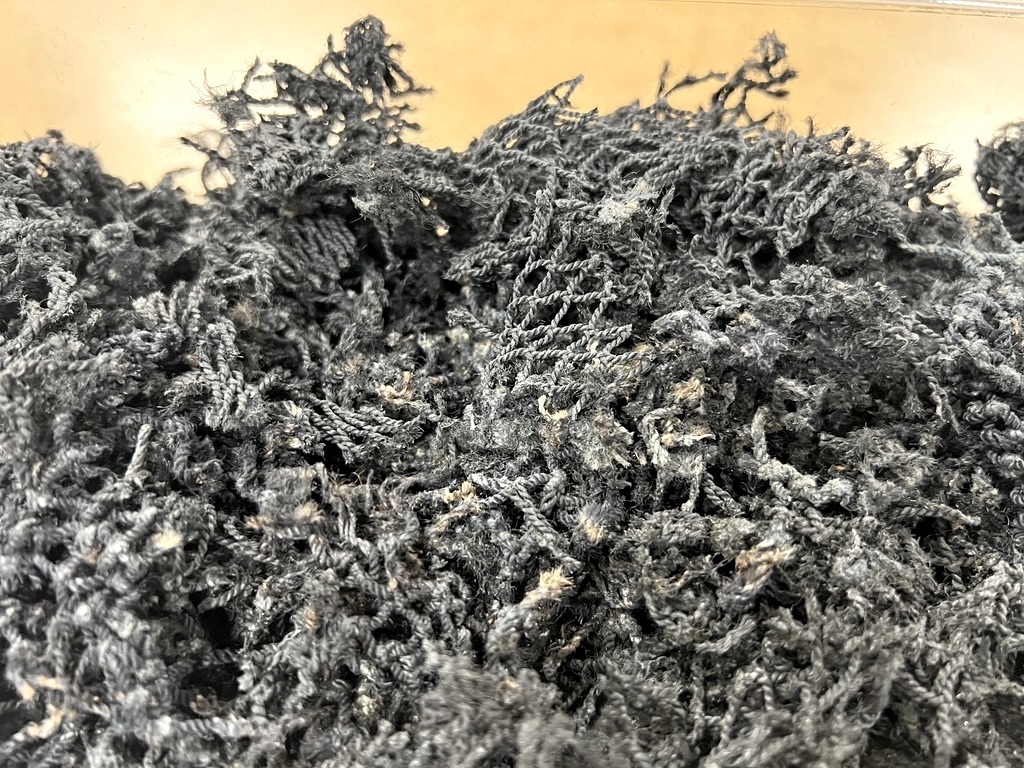
Discarded fishing nets are collected by Formosa Taffeta and then chopped up and chemically treated. Nets are made of Nylon 6 which can be broken down, and the nylon can then be reused and spun into new thread to be reused.
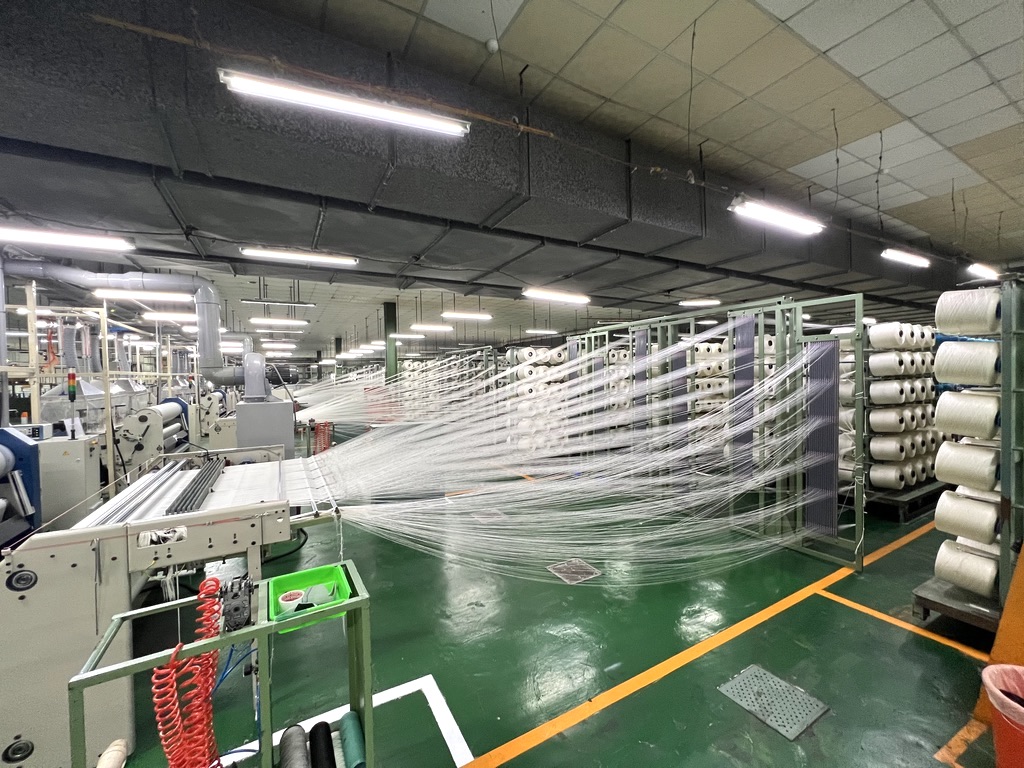
By utilizing the recycled raw material there’s a 49% reduction in CO2 emissions and 25% less energy consumption, as well as saving ocean life that could get caught up in the old nets.
Formosa Taffeta production is spread across Taiwan, China, and Vietnam. The Taiwanese operations make the thread in one factory while they knit it into giant rolls of fabric in another factory. Their production is on a massive scale with huge lines all running together to produce 750 tonnes of fabric per month.
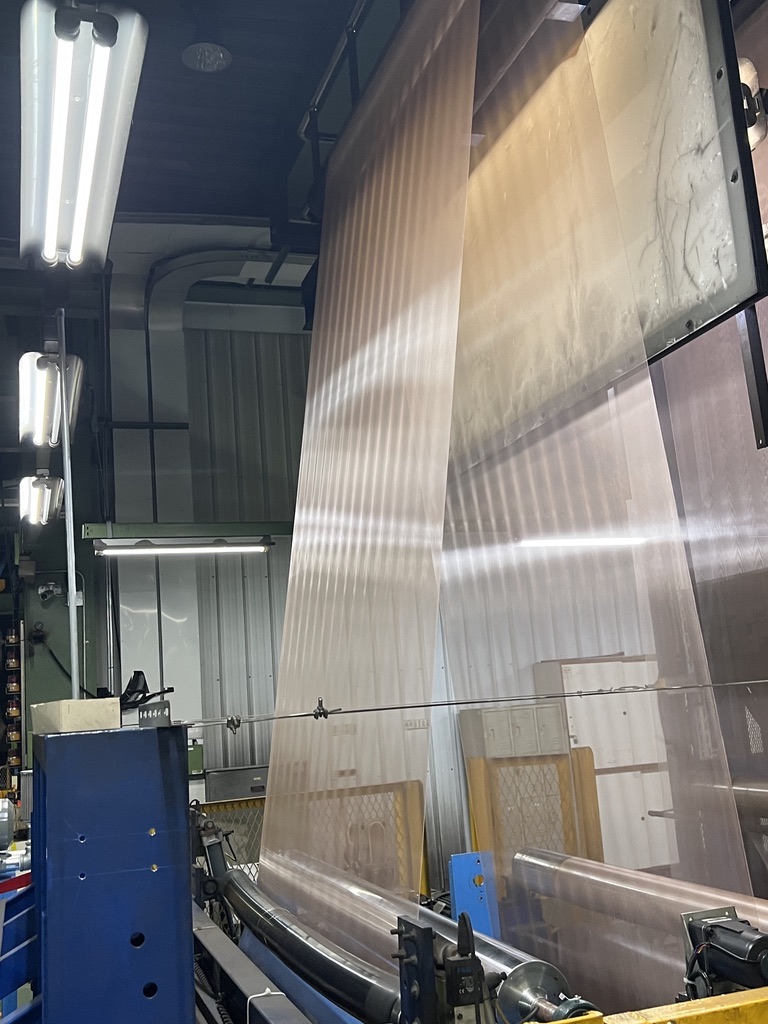
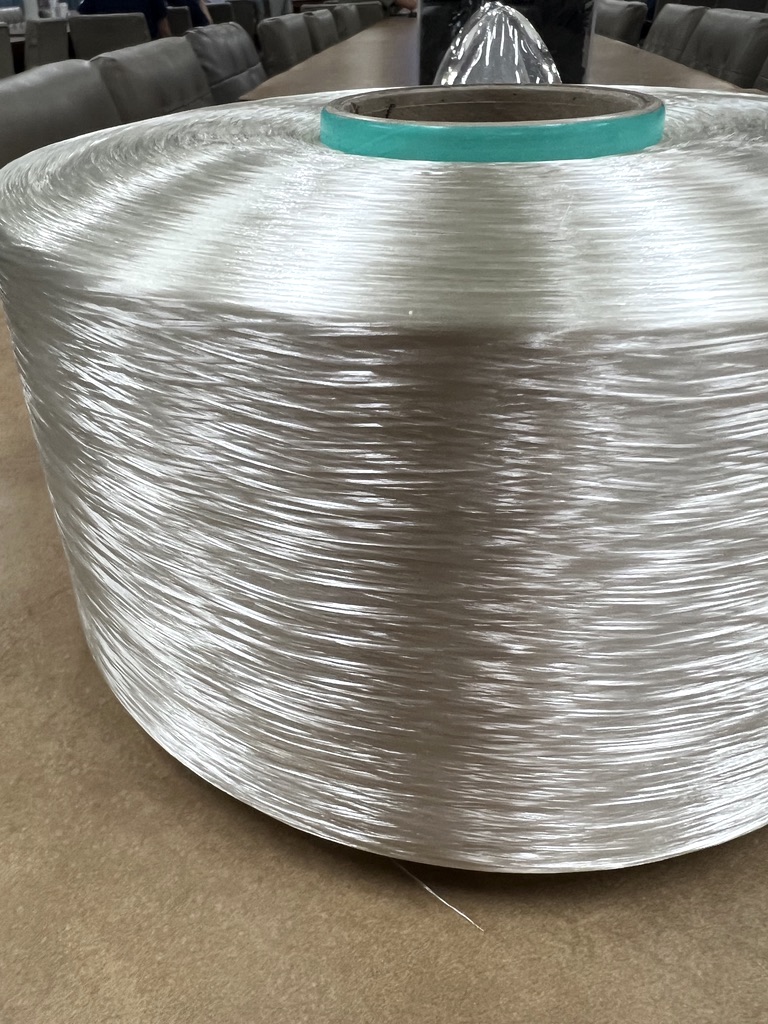
Sports fabrics account for 85% of their sales while the bicycle tire industry, which is a growing segment, accounts for 20% of their sales.
As a supplier to most cycling tire brands they provide the fabric layers which are used in the tires as well as the beading and have partnered with Maxxis to use recycled fishing nets in the cording process to make “greener” tires.
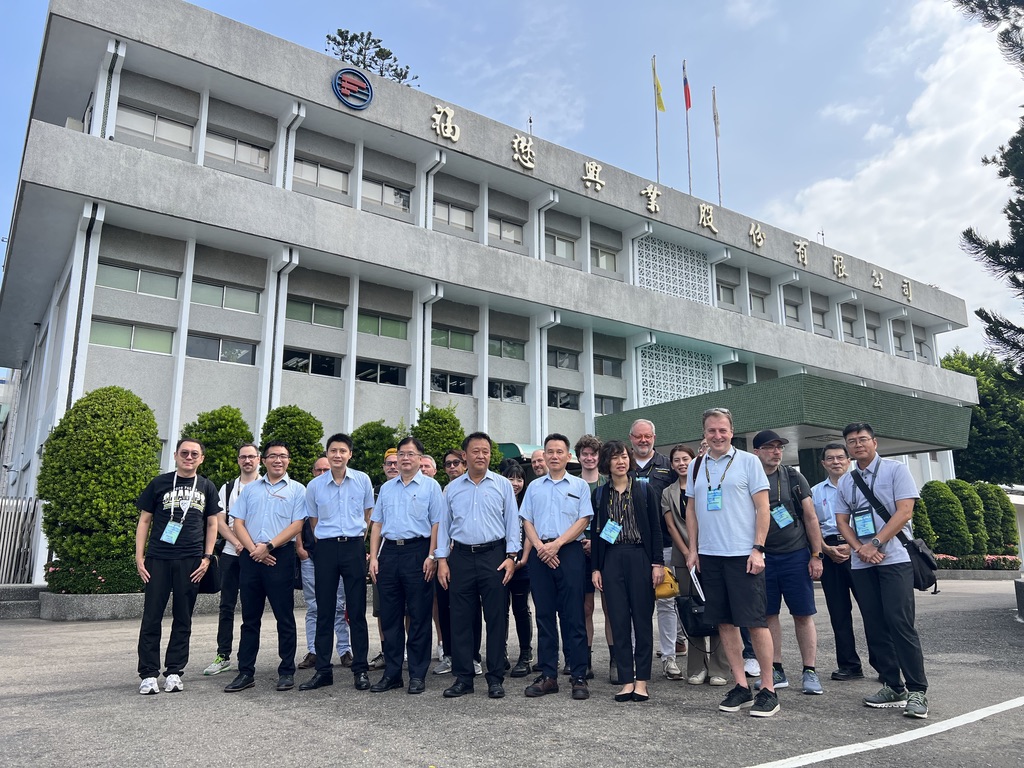
On top of these environmental efforts in their production, all of Formosa Taffeta’s factories have solar panels on their roofs as further recognition of their ESG steps to achieve sustainability.